Have you ever wished there was an easily-sourced decorative panel that was a natural “go-to material” for all of your interior, furniture, and fixture designs? A proven, reliable, and easily-sourced backbone for your hospitality, healthcare, office, retail, and even multifamily housing projects? One that didn’t break the bank, but still offered a wide range of contemporary and classic woodgrains and colors, with exact matches in other complementary materials?
And while we’re at it, why couldn’t this material be the “greenest” option out there, actually certified to be better than carbon neutral and deliver the in-demand visuals of rare and fragile raw materials without actually having to harvest them?
Seems a bit like wishing for the moon, with a fair bit of the rest of the universe thrown in.
Well, count your lucky stars. The material you’ve been looking for has actually been a staple for furniture and interior millwork for decades, but has recently been given new life thanks to advances in decorative printing technology and a groundbreaking life cycle inventory analysis.
And chances are it’s been part of your projects all along, used, or substituted as a favored material for furniture and millwork fabricators.
Thermally fused laminate (TFL) decorative panels are hybrid materials that combine the proven performance advantages of high pressure laminates (HPL) with streamlined manufacturing processes that minimize costs and resource use.
a brief history of tfl
TFL is a European creation, developed over a quarter century ago by large composite panel producers looking for a way to create decorative panels for furniture and interiors more efficiently than what was state of the art at the time: HPL glued to particleboard or MDF.
These producers took the uppermost decorative and durability layers of an HPL sheet, thermally fused them directly to the surface of the composite wood substrate, and marketed them as “melamine boards”—melamine being the resin system that gives toughness and clarity to the surface layer.
But the décors chosen for this first generation of TFL were pretty dull—white, almond, and grey. Black was introduced later with much fanfare. This is why for the first few decades TFL surfaces were used only for cabinet interiors, closet organizers, student furniture, and other applications where price point was paramount. This is also why many in the design community could be heard saying (not surprisingly), “Melamine boards? They’re great for cabinet interiors, but that’s about it.”
In the 1990s, TFL design began to emerge from the shadows. A handful of North American producers began to purchase décor papers from HPL suppliers, so designers could value engineer projects without compromising design harmony—the HPL on the high-wear work surface was now an exact match to the TFL casework.
Such design matching programs are now the norm, with all major TFL producers publishing cross-reference guides for matching and complementary designs in HPL, 3DL (three dimensional laminates), edge treatments, and other materials. This “one-stop-shopping” access to matching designs has played an important role in the growing use of TFL.
But probably the single largest driving force in TFL’s progress in the last 20 years is the advent of laminate flooring. Laminate flooring continues to grow as an option for durable, attractive flooring in residential and commercial installations, and by now pretty much everyone knows about the wide array of click-together flooring options available in the market today.
What few people realize, though, is that the vast majority of laminate flooring, including all of the brands that are now household names, is actually TFL.
Creating and refining a material fashionable and durable enough for the flooring market required years of innovation. The result is an extremely stable and durable decorative panel with enhanced impact and moisture resistance, high wear-resistant overlays to protect the decorative layer, and high-precision fabrication technology.
From global success in the flooring markets it was a short leap for TFL producers to return to furniture—now with a material that bears little resemblance to the white-almond-grey commodity panels of yore.
anatomy of a decorative panel
When you dive into the details (which we’ll do on the next page) the many advances made in the last decade alone add up to a much different material than the original “melamine boards,” but the basic structure remains the same.
TFL is a two-component material composed of the surface and core. The core is always composite wood, either particleboard or MDF, and the surface is a resin-saturated printed décor paper. For very high-wear applications (like flooring), an additional durability overlay may be used.
The secret to TFL’s appeal for responsible design lies in how these two elements are brought together. The resin systems in both the composite wood core and the décor paper overlay flow into each other and crosslink, or “fuse,” under heat and pressure in a high-tech press. This creates a permanent bond without the need for adhesives; the paper literally becomes part of the board, and will never delaminate.
Décor papers deliver the visuals: HPL, TFL, and the lighter weight paper-based foils all begin with a design concept, interpreted and executed by décor printers, who print on papers engineered to accept water-based inks used in the giant rotogravure printing presses, which absorb the reactive resins required in the pressing stage without degrading the print.
PageBreak
Design concepts for laminates come from an infinite number of places, and with today’s technology, the printed realizations of materials found in nature, industry, architecture, or even in the imagination, are stunningly vibrant. Special pearlescent inks can recreate the reflective flare of a piece of finely finished wood as you turn it in your hands.
Rotogravure printing: The rotogravure printing process involves laying down portions of a design in stages with up to four engraved cylinders, each carrying a different color water-based ink—the same process used for making fine art prints. Laser engraving of the cylinders enables greater print definition and detail in even the most subtle designs, as well as sharper contrasts and smoother tonal gradients for greater dimensionality and realism.
Printers work with artists to source the raw materials (original art, veneer, stone), which are photographed or scanned and digitally manipulated for scale and pattern repeat. These designs may be further tweaked for specific colorways, so the same visual structures may be offered in very different tones, creating a catalog of literally hundreds of designs from a single supplier.
Saving endangered trees: By capturing high-definition images of rare and exotic woodgrains for use in TFL, producers are helping to reduce the demand for those solid woods and veneers. Having access to those beautiful visuals allows you to design with some of the rarest woods in the world without the extravagant costs of harvesting and shipping, and without the inherent inconsistencies of color and character you encounter with the natural materials.
You’ll also be giving your clients much more durable surfaces for their commercial spaces. Nothing’s more heartbreaking than seeing gouges in a beautiful wood panel in a hotel that’s only been open for a few months.
After printing, décor papers are saturated with a melamine resin system that allows them to be laminated to the composite panel core. Melamine resins are extremely durable, heat resistant, and transparent after curing. They’ve been used for decades to create many consumer products. (Remember those indestructible light-green or beige lunch trays we all had in school that kids are still using? Those were made from melamine resins. So are many of today’s kitchen utensils.)
composite wood panels are better than carbon neutral
Particleboard and MDF panels are nothing new. Or are they? Thanks to the California Air Resources Board (CARB) standards, board producers have stepped up and modified their products accordingly. Composite panels produced in North America now meet, and usually exceed, these newly established indoor air quality (IAQ) goals.
Producers have also invested in further research into the true impact of their materials and their operations. Through a recent lifecycle inventory analysis (LCIA), they discovered something extraordinary—that their materials are actually better than climate neutral.
PageBreak
One major factor in this finding has more to do with the traditional makeup of the panels than recent modifications. Particleboard, as the name implies, is made up of small wood particles. In MDF, the wood chips are further refined down to cellulosic fibers, producing a panel with a smooth surface and homogenous core. Together they represent the highest level of evolution in maximizing the use of wood fiber left behind by other manufacturing processes from lumber mills, plywood plants, and furniture fabrication—wood fiber that would otherwise be burned or landfilled—as well as recycled post-consumer urban wood.
North American composite panel producers commissioned a life cycle inventory analysis of particleboard and MDF, taking into account all inputs and outputs required to manufacture these products, from the College of Forestry, Wood Science and Engineering at Oregon State University.
The analysis began with the generation of the forest, through harvesting, examining delivery, product manufacture, use, and disposal (whether to landfill, fuel use, or recycling). All inputs are measured, including electricity, fuels, chemicals, and materials used, from their in-ground resource through extraction, delivery, and manufacture. Outputs measured include product, co-product, and emissions to air, water, and soil.
A summary of the LCIA findings:
Composite wood panels make incredibly efficient use of resources:
• They consist of mostly recycled or recovered wood fiber. (some suppliers offer up to 100 percent non-virgin fiber content)
• Particleboard, over 90 percent.
• MDF, over 80 percent.
• 7 percent of the fiber is used as fuel in the manufacturing process.
• Less than 3 percent is landfilled.
Wood is one of the planet’s most easily renewable resources:
• Composite wood panels are primarily produced from wood resources that are sustainable, renewable, and recycled from pre-consumer waste, and can be made from post-consumer waste.
• U.S. forests are sustainable in that they generate more wood annually than are harvested; in 2006 there was 72 percent more net growth than total removals.
• To ensure wood is from specific sustainable sources, producers can request certification by such third party groups as FSC (Forest Stewardship Council), SFI (Sustainable Forestry Initiative), ATFS (American Tree Farm System), and CSA (Canadian Standards Association).
Composite panels are better than carbon neutral because wood is actually a carbon sink.
• Wood stores carbon as it grows.
• 50 percent of wood’s chemical structure is absorbed carbon, which is not released back into the atmosphere until it burns or decomposes.
• The carbon sink properties of the wood in composite panels more than offset its carbon footprint, including manufacture and transportation.
• Their net carbon footprint, therefore, is negative, actually offsetting some of the CO2 in the atmosphere.
• The longer a wood-based decorative panel lasts in an application, the longer that carbon is sequestered.
Given this new data, it’s more clear than ever that composite panels are more environmentally friendly than other commonly specified materials, like steel, cement, plastic, and glass, in that:
• They use significantly less amounts of fossil fuels and feedstock, water, and other resources.
• They beneficially use more renewable wood fuels, displacing fossil-fuel use.
Composite Wood Panels and Resource Efficiency
emissions
The benefits just discussed are what you might call the minimum baseline for composite panels produced in North America. Some suppliers take their environmental stewardship one step further with vertical integration—managing their own forestlands, logging operations, and value-added timber processing in communities where logging has been a way of life for generations. These traditional, often family-run or closely-held companies nurture their communities and resources for the long-term health of the environment, which means finding more ways to use as much wood fiber as possible.
This is the kind of thinking that helped streamline composite panel production in the first place. As the size of available trees began to diminish in the 1970s, some of these traditional companies refit their mills to handle the smaller logs. As the economy faltered they also diversified, adding particleboard and MDF production to make use of the waste produced by their sawmills and plywood plants. These manufacturers also began to grind up discarded furniture, palettes, and other deconstructed wood products to recover even more fiber that would otherwise go to landfill.
And they invested in biofuel technologies to use the small amount of leftover fiber as biofuel to cogenerate power for production, reducing the need for fossil fuels and reducing landfill waste to nearly zero.
application-driven engineering
Particleboard and MDF panels are produced by mixing the wood particles or fibers with resin, paraffin wax, and other additives, forming the panel, consolidating, and curing it under pressure and heat, and then sanding and sawing to desired dimensions.
The composite panels are highly stable, dimensionally consistent, and can be engineered for special performance properties:
• Moisture resistance
• Fire resistance
• Specific indoor air quality goals
• Density/screw-holding power
• Different thicknesses and dimensions
• Weight requirements
PageBreak
TFL is the most efficiently manufactured decorative panel. The process of thermally fusing the resin-impregnated decorative paper to a composite panel core takes less time than producing a sheet of HPL. In most cases TFL is pressed in the same facility that produces the composite panel, eliminating costly transportation and handling, and potential for damage. This means that the decorative panel leaves the factory with decorative surfaces on both faces, ready to be made into finished products or installed as decorative millwork. (HPL, on the other hand, must be glued to the panel in an extra production step, adding time and cost.)
Have your fabricator add an edge treatment and it’s ready for office desks, bistro tables, retail fixtures, nightstands—you name it. And with the ability to mix and match surface design, surface durability, and core properties, TFL decorative panels have few peers for furniture and interior design specification.
ecc qualification and leed credits
The Composite Panel Association, representing board producers across North America, has created a new voluntary standard for composite panel producers: “Eco-Certified Composite” (ECC). To qualify, individual manufacturing plants must first comply with the stringent California Air Resources Board (CARB) formaldehyde emissions regulation.
In addition, the composite panel manufacturing plant must meet at least three of the following requirements:
• Carbon Footprint
The plant must demonstrate that the panel’s carbon store offsets its cradle-to-gate carbon footprint as determined in kg-CO2 equivalents of greenhouse gas (GHG) emissions.
• Local and Renewable Resource
At least 85 percent of total annual wood fiber used must be sourced within 250 miles (402 km) of the manufacturing plant.
• Recycled/Recovered
The plant must use a minimum of 75 percent recycled or recovered fiber; or, at least 50 percent recycled or recovered fiber and a minimum of 5 percent post-consumer fiber.
• Sustainability
The producing plant must document that greater than 97 percent of its fiber furnish is either converted into panels or other non-waste products.
• Wood Sourcing
The plant must hold a valid assessment and certificate from a certifying agency recognized by the CPA such as the Forest Stewardship Council (FSC-Controlled Wood Standard or Chain of Custody Standard) or the Sustainable Forest Initiative (SFI—Fiber Sourcing Standard).
TFL+ Environmental Responsibility
There are many ways to measure the environmental impact of a decorative panel. There’s the scientific approach, as in the LCIA, and there are the harder-to-measure factors:
Efficiency: TFL is very efficient to manufacture, displacing the additional processing energy and chemicals required by other materials.
Durability: TFL is longer lasting and easier to clean and maintain than veneers and other materials.
Responsibility: TFL replaces fragile and exotic solid woods and veneers that are easily damaged—a major advantage, particularly in commercial and hospitality applications.
Too many projects use solid woods or veneers in high-abuse applications where they’re quickly scratched, dented, or gouged. Not only is this an egregious waste of wood; it also brings down the perceived value of an entire project. Worse, replacing wood or veneer with the same character and color of the original is nearly impossible because the variety of natural character and natural changes in color after installation.
For all of these many reasons, a growing number of designers recognize the value proposition of cost, durability, and design of TFL as the preferred decorative laminate for their projects.
The ECC Finished Products certification program is for laminators and fabricators of finished products such as TFL. It builds on ECC compliance for panel products and provides an audited chain of custody so ECC-compliant products can be tracked right through to the consumer.
Facilities certified as ECC must demonstrate that at least 50 percent of the content of any product they laminate or fabricate is made with ECC-compliant panels; plus, of the total composite panels used, at least 95 percent of the composite panels must be ECC-compliant.
ECC Panels may help achieve LEED (v2009) Credits for:
• MR 4.1 and 4.2: Recycled Content
• EQ 4.4: Indoor Air Quality (No Added Urea Formaldehyde)
• MR 5.1 and 5.2: Regional Materials
• MR 7.0: Certified Wood (FSC Certified)
ECC Value Added (Laminated) Products may also help earn:
• Low Emitting Materials EQ Credit 4.5 (LEED–CI)
This article is advertiser sponsored
In preparation for the market transition to LEED v4, composite panel producers have adjusted resin formulations to meet tighter indoor air quality standards (Ultra Low Emitting Formaldehyde—ULEF and No Added Formaldehyde—NAF). Producers have also sponsored the development of Environmental Product Declarations (EPD) for particleboard and MDF. These industry-wide EPDs are available to the public through the American Wood Council at http://www.awc.org/greenbuilding/epd.php. As other adjusted credit categories in LEED are clarified, expect composite wood producers to provide practical and applicable information to the market to support these and other green building standard requirements.
matching material programs
Even as advantageous as TFL panels seem to be for so many uses, producers realize that you might want to value engineer other materials into your projects. This is why TFL suppliers will share décor papers and design files with HPL, 3DL, lightweight paper, and edgebanding suppliers for exact surface matches and offer specifiers cross-reference charts to take the mystery out of designing with matching or complementary colors and structures.
the long future of tfl
The most successful projects happen when all of the stars align; you’re able to use materials with designs that delight the client, offer aesthetic harmony with complementary materials, are tough enough for the application (but not overkill), meet your “green” goals, and work with the budget you’ve been given.
Decorative TFL panels give us the option to design without guilt, leaving as many trees as possible where they belong—absorbing carbon, emitting oxygen, and helping us all breathe a little easier.
About the Author
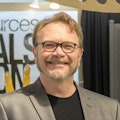
Kenn Busch
Contributing Editor
Kenn Busch is a longtime journalist, educator and public speaker dedicated to bridging the knowledge gap between materials, sustainability, and furniture and interior architecture. He is the founder of MateralIntelligence.com and ClimatePositiveNOW.org, two major resources for design and manufacturer specifiers.